会员登录
MEMBER LOGIN
技术论坛
TECHNOLOGY FORUM
高强度厚大断面球墨铸铁机床件铸造 工艺关键得当
发布时间:
2016-04-25 00:00
来源:
《金属加工(热加工)》
高强度厚大断面球墨铸铁花盘的铸造工艺设计过程。采用无冒口铸造工艺技术,数值模拟技术,专用石墨冷铁强制冷却工艺,快速充型技术,特殊制芯工艺,增强补缩效果的浇注系统,中频感应电炉熔炼工艺等关键工艺技术,成功生产出了优质铸件。
1.铸件特点和技术要求
重型数控4.5m卧式车床是我公司为一重集团自主研发的重点产品,其花盘是机床的关键件,由于铸钢件加工困难,缺陷多,所以选用了高强度球墨铸铁材质,铸件重40t,属厚大断面球墨铸铁件,结构尺寸如附图所示。铸件特点及技术要求如下。
(a)
(b)
(c)
花盘结构
?。?)铸件材质QT600—3,机加后硬度要求不低于180HBW?;С煞?、力学性能、金相组织等各项技术指标要求非常严格,要求对附体试块进行各项指标的检验。
(2)平均壁厚185mm,铸件模数为7.81cm。要求进行超声波无损检测,内部组织不得有缩孔、缩松、气孔、夹渣和冷隔等缺陷。不得有尺寸、化学成分、力学性能不合格及裂纹缺陷,不能放置芯撑。外观和内腔不得有粘砂、绕曲变形缺陷。但这些缺陷正是厚大断面球墨铸铁件极易出现的。
?。?)铸件重量大,尺寸大,壁厚大,因而熔炼浇注的技术难度大。
(4)在双层壁与单层壁结合处(见附图d),是铸件应力集中处,易导致铸件产生裂纹缺陷,给铸造带来很大难度。
?。?) 铸件加工后要求做静平衡试验,因而对砂芯的尺寸一致性、分度和定位尺寸要求非常精确。
2. 铸造工艺设计
根据对铸件特点和技术要求的分析,确保工作台面的质量和铸件尺寸精度,方便下芯及砂芯固定,使各工序操作方便,依据厚大断面球墨铸铁件在凝固过程中石墨化膨胀,可有效自补缩的特点,同时配合使用专用石墨冷铁强制冷却,采用无冒口铸造工艺方案,两箱造型,铸造工艺如附图b所示,并使用华铸模拟软件进行了模拟。
(1)防止产生裂纹缺陷的措施 为防止铸件产生裂纹缺陷,在单层壁与双层壁结合处的每一个卡爪槽上端设置了3道防裂工艺拉筋,在砂芯上做出。打箱时铸件温度控制在100oC以下。打箱清砂后,马上进行消除应力退火,其保温时间和冷却时间适当延长,工艺拉筋由机加工切掉。
?。?)主要工艺参数、砂芯设计、砂种及涂料 制作Ⅰ级木模,芯盒强度好,尺寸精确。缩尺10‰,加工余量:分型面处+25mm,侧面+15mm,主轴孔及卡爪槽+15mm。起模斜度 5mm,砂芯间隙2mm,分型负数-4mm。铸造圆角R15mm。设计了6个卡板,测量砂芯的尺寸精度、分度及定位尺寸。砂箱吃砂量400mm,合箱后用M48螺栓紧固砂箱,并在中间捆一道龙门压梁,以确保砂型刚度。设计了17块砂芯,2#~9#砂芯与下箱把合牢固,10#~17#砂芯与上箱把合牢固,因此不用放置芯撑。采用冷硬呋喃树脂自硬砂造型制芯,砂型24h强度不低于1.1MPa,选用醇基锆英粉快干涂料,型芯舂实,涂料均匀涂刷两遍。砂型强度高,刚度好,保证了无冒口铸造工艺对砂型的要求。根据型内测温,打箱时间为30天。
(3) 强制冷却工艺 为平衡壁厚差,控制凝固顺序,达到或接近均衡凝固,并参考数值模拟结果,采用专用石墨冷铁强制冷却工艺,消除因壁厚过大且不均匀带来的热节效应,即可防止厚大断面心部产生缩孔、缩松缺陷,又可使石墨化膨胀提前发生,增强自补缩效果,共设计了12种专用随形石墨冷铁。
?。?)制芯工艺 全部砂芯采用特殊制芯工艺,焊制了专用芯骨,在专用石墨冷铁上做出M12螺孔,拧上螺丝杆,在芯盒中固定好位置后与芯骨焊接牢固,再填上砂子舂实,以保证石墨冷铁位置准确和砂芯的尺寸精度。石墨冷铁覆盖面积达铸件散热面积的95%以上。石墨冷铁可以重复使用4次。
3.浇注系统和冒口的设计
根据铸件特点,采用大孔出流理论,铁液大流量快速平稳充型,铸型温度场均匀,设置3层阶梯式内浇道,环形横浇道,避免铁液在型内发生旋转、扰动,使铁液尽快静止,以便尽早发生石墨化膨胀,提高自补缩效果,两台浇包浇注,最上层内浇道距分型面50mm,以便补浇时能很好地补充铁液的液态收缩,浇注重量 。
?。?) 浇注时间 的计算 取系数 ,最小壁厚δ=60mm
(2)平均压力头Hp的计算 以直浇道下口为阻流截面。
Hp=H0-(p2/2C)=60-(02/2×735)=60cm
式中:H0 — 阻流截面以上的压力头(cm);
p — 阻流截面以上的型腔高度(cm);
C — 铸件型腔总高度(cm )。
(3)计算阻流截面积 取流量系数 。μ=0.5
ΣF阻=G/(0.31μt Hp )=44000/(0.31×0.5×159×60)=230.5(cm2)
(4)计算各组元截面积 采用半封闭式浇注系统,确定各组元截面积比为ΣF直:ΣF横:ΣF方直:ΣF内 =1:2.5:2.2:2,浇注系统可充满,充型快速平稳,阻渣效果好。
ΣF横=2.5×230.5=576.25cm2
ΣF分直=2.2×230.5=507.1cm2
ΣF内=2×230.5=461cm2
共设置50个25mm 50mm直形明出气冒口,使用两个铁液容量为2t并设有阻渣闸板、浇口塞及定量瞬时孕育漏斗的浇口杯。
确定各参数后,经过再次数值模拟分析,确定了整个工艺方案是可行的。
4. 熔炼及浇注工艺
?。?)根据铸件特点和技术要求,采取了加铜的合金化措施,操作简单方便,效果好,目标化学成分:wC=3.5%~3.6%、wSi=2.3%~2.5%、wMn=0.6%~0.7%、wP≤0.05%、wS<0.02%、wCu=0.6%~0.7%、wRE=0.04%、wMg=0.05%。
?。?)使用两台20t中频感应电炉溶炼铁液,配有撒布浪斯NSP—6000型炉前快速成分分析仪,NSP—305MTX快速测温仪,OCS—XS(F3)无线传输电子吊秤,德国M20型直读光谱成分分析仪。
(3)强化原材料质量,原材料要求及加入量如附表所示。
球化剂、孕育剂使用前要烘干,严格控制化学成分。过热精炼温度1500oC,脱硫处理温度1420oC,球化处理温度1450oC。
?。?)两台电炉同时球化处理,球化处理结束至浇注时间间隔不得超过6min,要扒净渣。开始浇注后打开瞬时孕育漏斗进行定量孕育,待浇口杯充满时拨开浇口塞,开始快速充型,在规定时间内充满,浇满后再补浇两次。 浇注温度(1330 10)℃。
结语
由于工艺上采取了关键得当的工艺措施,解决了各项技术难题,首件铸件铸造成功。经对附体试块的检验,化学成分、力学性能、金相组织都达到了技术要求,经超声波无损检测,内部组织致密无缺陷,说明工艺方案是合理的。截至目前先后为一重集团、中信重工、沈阳黎明集团、江阴真良机械、东电集团生产了5件,合格率达100%,铸件品质达到同类产品国际先进水平,使我公司生产此类厚大断面球墨铸铁件的技术水平得到了很大提高。
附件下载:

-
地址:济南市解放路134号 电话:0531-86401781 / 86952422 传真:0531-86465075
邮箱:foundry-shandong@163.com 邮编:250013
版权所有 © 山东省铸造协会 鲁ICP备2021002429号
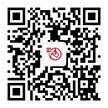
官方公众号