会员登录
MEMBER LOGIN
技术论坛
TECHNOLOGY FORUM
铝合金缸体压铸生产中机加成品表面孔洞产生原因及解决措施
发布时间:
2016-06-24 00:00
来源:
1 概述
缸体是发动机最为关键的 5C 件之一,发动机缸体一般为结构复杂的箱体件,使用性能方面,不仅有基本的尺寸形状和强度要求,更苛刻的是对气密性的要求。从铸造专业角度来看,压铸箱体厚壁件内部存在气孔、缩孔、渣孔在所难免,如果有气密性要求的位置刚好发生了孔洞缺陷,将引起报废;因此成品机加面孔洞问题是缸 体压铸所必须要解决的质量问题。 本文所讨论缸体采用高压铸造工艺生产,该缸体为直列四缸箱体结构,缸体壁厚相差较大 (3.5mm-22mm),水道、油道机构复杂,并设置独立的水泵安装孔及电机安装孔,相关部位对强度、密封性要求较高。本文所讨论的质量问题发生在水泵安装孔柱面密封带区域,直接影响水泵的密封效果,该问题导致产品报废率居高不下。本文对该缺陷产生原因进行系统排查分析并针对性的提出整改方案。
2 孔洞缺陷形成原因分析
2.1 孔洞缺陷形成原理
高速度、高压力是压铸成型工艺的两大特 点,因此压铸工艺的充型、凝固过程与传统重力铸造、低压铸造存在显著区别:充型、凝固过程极短,一般为几十到上百毫秒,几乎可以说是瞬时充型、瞬时凝固。这就决定了压铸过程常常伴随着不可控的紊流、卷气和夹渣,这也就不难解释厚壁压铸件内部普遍存在的气孔、缩孔及渣孔等缺陷的现象了。由于凝固过程的激冷效应,压铸件表面往往形成厚度为 1mm 左右的致密层,气孔、缩孔及渣孔等缺陷藏匿于压铸件内部,但铸件经机加工后,加工表层的致密层遭到破坏,内部孔洞暴露于表面,明显影响该面的密封效果,严重时将导致产品报废。
2.2 缺陷基本情况
本次影响产品质量的孔洞主要集中在曲轴箱水泵安装孔柱面密封带区域,呈孤立分布,直径在 1mm-2mm 之间,缺陷件数量约占生产总量的 8%(见图 1、图 2 所示)。从整个铸件及浇注系统来看,缺陷发生位置处于远水端,因此我们初步判定该缺陷与压铸充填过程中的排渣排气相关,在进行现场过程排查的同时采用 CAE 分析手段辅助方案制定。
图 1 缺陷图示
图 2 缺陷在产品中的位置
2.3 主要原因分析
2.3.1 CAE 分析
发生缺陷位置在浇口对侧,整体呈涡轮状,排气排渣相对难度较大,困气、夹渣的风险较大, CAE模拟结果也进一步支持我们的观点,该位置确实存在排气不畅的风险(见图 3);抛开产品结 构和浇注系统,排溢系统的设计很显然不是最优方案,CAE 显示该处卷气相对严重但周边排溢设计过于简单,无法达到理想的排气、排渣效果, 局部内部质量自然不理想。所以我们认为最简单 有效的整改手段即是优化该部位溢流槽、集渣包,在卷气位置、充填方向上增设溢流槽和集渣包,提高局部排气集渣效果。
图 3 CAE 分析(困气分析)
2.3.2 工艺排查结果
1)铝液温度及铝液含气量。采用电热偶对铝液进行温度监控,铝液保温温度维持在 660℃-690℃;采用密度当量仪每小时对铝液进行检测跟踪,铝液密度当量维持在 2 以下(DI 值),我们认为对于压铸工艺属于较理想的铝液。
2)模温平衡情况采用 FLIR 热成像仪对模具镶块进行定时拍照跟踪(见图 4),缺陷位置喷涂后,整体表面温度分布在 150℃-240℃,缺陷发生位置模温稳定在 180℃-230℃,属于比较理想的模温,且型腔内无水分残留。
3)压射参数情况 铸参数经过长期调试、已固化,我们尝试将压射速度提高以提高远水端的充型效果,增加压力以提高增加效果,结果铸件内部质量下滑十分严重,因而我们认为压射参数变更将带来更大的问题,原压射参数暂不考虑变更。
4)设备运行情况根据当月的统计,设备运行正常,设备开动率为 83.2%,属压铸生产正常水平,根据废件编号追溯,报废与设备停机无直接联系。
5)真空系统 根据当月跟踪情况,我们发现,缺陷发生与真空系统的运行,存在一定的相关关系,往往真空系统发生堵塞前生产的产品该问题发生率显著升高,超过半数报废发生在真空系统发生堵塞前 5 件,我们认为孔洞的发生跟真空系统故障或 运行的不稳定所导致的排气效果变差呈直接关系,这也进一步验证了 CAE 分析的结果。
2.3.3 分析结论
发生缺陷位置属于充型末端,充填上属于含渣、含气的较为集中部位,一旦该处排渣排气不畅,即导致内部质量变差,机加后表面致密层破坏,形成孔洞。 根据 CAE 分析结果,该处设计成涡轮状,且溢溜槽开设方向不理想,排渣排气效果不佳,在真空系统运行不稳定的情况下,排气效果进一步恶化,导致缺陷增多;另外,该处 1mm 的加工余量过大,造成表面致密层完全被破坏。
3 改进措施
我们根据上述分析、排查结果,结合我厂生产实际,针对性地制订了详细整改方案,全面优化工艺设计,加强过程管控;
3.1 根据 CAE 分析结果,优化排溢系统,困气部位增开渣包(如图 5 所示),提高该部位排渣排气效果;
图 5 溢流系统整改方案
3.2 通过专业培训提高车间使用、维护真空系统的能力,通过制定真空系统强制点检、定期维护,保证真空系统的正常运转,确保排气效果;同时加强过程控制,确保生产过程稳定可控;
3.3 保证机加质量的前提下,对该处加工余量进行适度削减,按单边 0.6mm 进行设计,以保 证该处加工时压铸致密层未完全破坏,达到降低缺陷暴露的概率(见图 6 所示)。
图 6 机加余量整改方案
4 结束语
通过系统的原因分析和排查,按照制定方案的严格推进和执行,该缺陷引起的铸件报废比率明显下降,由原来的 8%下降至 0.2%(占生产总数百分比),铸件整体良品率也上升至 94%以上, 这一问题得到了解决,顺利达成既定目标。从本次案例可看出,压铸生产过程中缺陷的排查与解决是系统问题,只有从产品、工艺、生产三方面逐项排查、逐项优化,才能较好地解决质量问题
附件下载:

-
地址:济南市解放路134号 电话:0531-86401781 / 86952422 传真:0531-86465075
邮箱:foundry-shandong@163.com 邮编:250013
版权所有 © 山东省铸造协会 鲁ICP备2021002429号
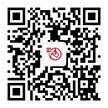
官方公众号