会员登录
MEMBER LOGIN
技术论坛
TECHNOLOGY FORUM
我国造型装备现代化的现状与问题
发布时间:
2016-07-07 00:00
来源:
根据中国铸造协会的统计,灰铸铁的95%、球墨铸铁的60%、普钢铸件的85%、合金钢铸件的80%都是用各种砂型铸造的,也即约76%的总铸件产量是用砂型生产的。这是因为砂型铸造具有悠久的历史,各个国家和企业对其有着丰富的经验和知识,同时其也是生产成本最低、效率最高的铸造方法。我国2014年的铸件产量已经到了4620万t,也就是说我国至今约有3500万t铸件使用砂型铸造,这与国际上的报道相似。
造型工序是铸造所有工序的核心,其他各个工序都是由它而定来相配的。造型能力的大小和水平也确定了一个铸造企业的规模和技术水平,因此在新企业设计与老企业技术改造时,都是从选择造型方法和造型设备开始的。
一、我国造型生产装备应用现状
技术的进步,用户对铸件质量要求(尺寸精度、减少机加工余量以及对铸件均匀性与一致性)的提高,迫使铸造业要向机械化、自动化生产转变。尤其今天,便宜劳动力的日子已经过去,铸造相对于其他机械制造工艺又是相对比较热、脏、累的工艺,年轻人不再愿意从事铸造工作,有些企业高价也找不到技术工人(有些地方的造型工月工资已在8000~10000元),因此迫使铸造企业走技术改造之路,使用机械化、自动化设备来减少工人的用量,提高劳动生产率,冲破了 “不改等死,改了找死”的观点,形成“不改等死,改了生存”的理念。为此在近五年自动化造型设备的市场非?;钤荆祷煨蜕璞甘谐∪战ノ?。表1是2011~2015年我国新上自动造型设备的不完全统计。由于生产树脂砂设备的企业很多,统计时对造型线的概念不清,不少企业报出的数据有点扩大,但其他的数据还是可信的,尤其是潮模砂造型线的数据,由于生产企业就有数的几家,应是十分可信的。
潮模砂适用于各种批量的中小件生产,在过去的5年中,我国新投了1203条自动线。如果有箱造型自动线的平均产量为3万t、垂直分型自动造型线的年产量为1.5万t、水平分型自动线的年产量在1万t,则这5年新增能力是1900万t。其他各种造型线,除了树脂砂线适用于中大件外,另外的造型线适用于一些特殊的铸件(例如,铁模覆砂非常适合于曲轴和球墨铸铁小件)。若按每种造型线的年能力为2500t保守值计算,则6种造型线新增造型能力是410万t。两者加起来,我国在过去5年新增造型能力2300万t,占需要量的66%。
一条造型线正常使用年限在20年以上,不少企业可使用30多年。因此要看我国造型现代化的水平还必须计算过去20~30年的装备投入情况,可惜我们缺少有关的统计。但有一点是肯定的,就是按装备造型线的数量和能力已远超过全国需要的能力。笔者曾根据不完整的统计估算出,2010年前我国已有4000多条各种造型线。有箱自动造型线是造型中最复杂、造型能力最强的造型线,也是我国至今还没有完全掌握的项目。表2是几个世界著名的有箱自动造型线的制造厂家,不计GF公司的气冲造型线,他们在2015年底前共销售了149条。而他们在2011~2015的5年中在中国仅销售40条,这表明60%以上都是在“十二五”以前销售的。又如保定维尔是我国最大的铸造设备生产商,至今已销售624条垂直分型造型自动线,而在近三年只销售277条,仅占44%,销售的静压线有54条,在近3年只销售17条,占31%。这都表明,我国所有投入的现代化造型线能力已远超过3500万t铸件的需要量。如果能让已经投入的造型线正常发挥作用,则可以生产5000万t的铸件。
二、我国现代化造型线应用中存在的问题
既然有这么多的现代化造型线,那么为什么现实中大家看到的,仍然有非常多的铸造厂停留在手工造型或简单的机械振击造型呢,这是值得我们去探讨的问题。
笔者认为原因有以下四个方面:
(1)有些投资者看到了铸造业要向机械化、自动化转型而愿意投资,但他们不愿意和已有的企业合作,认为只要建成了现代化的工厂就不愁没有订单。于是,他们在既无任务又无技术人员的情况下建厂?;钡厍幸晃煌蹲嗜耍鲎?亿多,建成了一个具有两条无箱自动造型线、两条树脂砂大件造型线、有起吊能力100t的现代化厂房,能力为5万t的铸造厂。结果是运行几年后,每年只有2~3000t的订单而不得不停产,投资失败,投资的造型线变成有统计而无产量。同样有一个单位,其自身拥有技术,投资了一条年能力为3~5000t的消失模造型线,结果也是只有几百吨的任务,造成资金链断裂而破产,造型线成了废铁。
?。?)在建新厂或技术改造时,不用正规的设计研究院而缺少全面的规划,造成铸造各个重要工序之间的能力不配套,发挥不了造型线的能力。1993年进行的调查表明,当时的造型线开动率平均是49.7%;2012年调研得到的造型线开动率是56.9%;中国铸造协会曾对24个大型铸造企业的51条造型线进行过调查,其中49条线是进口自动线,结果是平均利用率为62%,最高的92.86%,最低的仅27.4%,利用率太低。
国外的铸造企业,其造型线的利用率要求达到85%以上。DISA公司报道,用他的垂直分型造型自动线生产刹车盘铸件的利用率达到93%。韩国在江苏的一家铸造厂,其用DISA线生产刹车盘,利用率在92%以上,现在正提出向93%进军的目标。这里也反映出我国铸造企业的精益管理差。国外企业的造型线在使用时必须按开动率和利用率来记录造型线的运行情况,用SPC方法分析利用率提不上去的原因,采取相应的有效措施,使造型线充分发挥作用。
现代的造型线本身就带了停机记录功能,但其功能并不能显示?;脑?,还必须要人去补充。此外,在向自动化、数字化、智能化过渡中,造型线已经带有各种调整功能,使造型线在运行时可选用适合于每一种个性化铸件的最佳参数。例如现代的静压造型线,其是否要用预紧,使用时用多少压力、多长时间,压力紧实时多触头压力圈及其压力大小的选择,后续浇注时间、浇注重量的选择,以及随流孕育量和时间的选择,都可以按不同的铸件选用不同的参数,最后输入到控制系统中储存并反复使用。这样做不仅有利于提高最终铸件的质量,节能,而且也可提高造型线的利用率,因为70%左右的铸件是不需要预紧的。其实,这也是精益生产的一个重要部分。
?。?)我国铸造企业的集中度不够,或铸造企业规模太小。我们可以看到许多企业在原有手工操作的基础上进行了技术改造,采用了造型自动线,在运行中也体会到了机械化、自动化对提高质量和降低生产成本的好处,但由于自身产量不大,又不能所有的铸件上线,因此提不高造型线的利用率。一条潮模砂的自动造型线,其能力都在1万t以上,而许多年产5000~6000t的铸造企业使用了造型线,只能降低生产率或一班运行。
?。?)企业的维护和保养能力差。自动造型线总会在运行中产生一些故障,虽然现代的设备装有远程诊断系统,但企业自己还是要有一支较强的技术队伍来解决一般问题。现在的铸造企业连铸造本身的技术人员都不够甚至没有,就更顾不上设备维护人员了。因此,一出问题就要等制造商过来,利用率当然也无法高上去。
从理论上讲,我国造型线的数量已经够用,但实际上我国造型线的现代化水平和国外先进国家相比还相差很远,这必须在今后铸造业的转型中加以改变。但这种错位发展也给我国铸造装备业带来了生机,这也是近十年设备制造企业日子相对好过的原因。但为了铸造事业的发展,铸造装备业也必须看到自身的问题而
附件下载:

-
地址:济南市解放路134号 电话:0531-86401781 / 86952422 传真:0531-86465075
邮箱:foundry-shandong@163.com 邮编:250013
版权所有 © 山东省铸造协会 鲁ICP备2021002429号
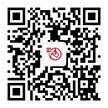
官方公众号