会员登录
MEMBER LOGIN
技术论坛
TECHNOLOGY FORUM
大型球墨铸铁机床件铸造 三步处理法
发布时间:
2016-02-23 00:00
来源:
我公司铸铁厂年生产能力铸件3万t,以大中型铸件生产为主。自2008年投产以来主要生产风电铸件、大型机床件、注塑机模板、核电机壳、各种缸体等。在大断面球墨铸铁铸件的生产中也积累了雄厚的技术基础,在同行业和客户中获得了良好的口碑。
近年,我分公司发展再上新台阶,与国内一些著名企业结成了战略合作伙伴关系,如三一集团、陕鼓集团、杭州创研、海天集团、沈阳机床、中国一重、中国二重、上海迎风等核心客户,形成了单件铸件超过了120t的生产能力。
我公司为沈阳中捷机床厂生产的立车横梁VMG6(13150mm×2000mm×1100mm),毛重87t,最大壁厚300mm。此机床为沈阳机床厂引进德国技术生产,由德国工程技术人员负责图纸设计及后期装配完成,对铸件外观质量、内在质量要求较高,材质为GGG-40-15(相当于我国QT500—7),导轨硬度175-250HBW,球化等级大于3级,厚大断面组织为铁素体+珠光体,是标准的大型球墨铸铁件。
熔炼设备:20t+40t中频感应电炉。
浇注设备:25t+40t铁液包球化处理浇注。
造型工艺:呋喃树脂砂砂箱造型。
补缩工艺:外冷铁+自补缩。
容易产生的问题:球化衰退、石墨漂浮、碎块状石墨、反白口、缩松、缩孔,以及中心部位石墨球数减少等。
?。? 原辅材料选用
?。?)选用优质高纯生铁。生铁应属共晶成分,可避免生成过共晶的粗大石墨。微量元素总量(质量分数)≤0.1%,Ti≤0.04%,微量反球化干扰元素的总量<0.1%。
干扰元素分为两大类,一类是消耗球化元素型干扰元素,例如S;另一类是晶间偏析型干扰元素,包括Sn、Sb、As、Cu、Ti、Al等。在共晶结晶时,这些元素富集在晶界,促进碳在共晶后期形成畸形的枝晶状石墨。
由于磷既显著升高塑-脆转变温度,又强烈降低球墨铸铁的上限冲击吸收功,对球墨铸铁的脆化危害作用主要是形成磷共晶(三元磷共晶、二元磷共晶),所以成为裂纹的发源地,同时加剧球墨铸铁的缩松倾向。国内产自本溪和林州的生铁干扰元素少,纯净度高,故适合生产大型球墨铸铁铸件。
?。?)废钢选用纯净低锰、低磷、低硫无铁锈的碳素钢,如A3钢、45 钢等。
(3)球化剂选用钇基重稀土球化剂和轻稀土球化剂,轻稀土球化剂包括珠光体球化剂和铁素体球化剂。
?。? 化学成分要求
生产高性能厚截面球墨铸铁件,选择适当的炉料是控制铁液化学成分的第一步,这对于控制铁液的冶金特性是非常重要。生产中S、P属于限制性元素,要求,wS≤0.015%、wP≤0.03%
过低的C含量会使塑-脆转变温度区间向高温反向偏移,影响低温冲击值。所以在不出现石墨漂移的情况下,尽量取高的C含量。
碳当量的选择范围即要保证充分石墨化的要求,又要考虑发生石墨漂浮的风险。为获得良好的补缩性能和键全的铸件,一般將其选在共晶点(CE4.3)附近或稍许亚共晶成分。
碳当量控制在CE=4.2%~4.3%,主要调整C、Si含量基本不变。
3.铁液的预处理和过热处理
炉内预处理剂是一种含氧、含硫的新型孕育剂。这种孕育剂加人铁液后,铈﹑钙与孕育剂本身所含的硫和氧反应,也与铁液中残留的硫和氧反应。使铁液中的含硫﹑氧量更低。这些化合物在1500℃左右是稳定的,粒度约为1~3μm,密度约为6.5g/cm?。炉内预处理剂基本上呈球形,可以弥散分布于铁液中,作为石墨的外来晶核。如果运用得当,將含硫、氧的孕育剂用于球墨铸铁,可以多方面改善球墨铸铁的性能。如:
?。?)石墨球的尺寸减小,数量增多,球化率提高。
?。?)减轻铸铁的白口倾向,有利于制造薄壁球墨铸铁件。
?。?)生产厚壁铸件时,可减轻晶间偏析,提高铸件质量。
?。?)生产厚壁铸件时,可减轻或防止石墨漂浮。
(5)减少铸铁凝固过程中的收缩,铸件产生缩松、缩孔的倾向小。
?。?)可减少15%~30%球化剂的加入量,提高镁的吸收量。
铁液过热温度1500~1520℃。停电静置5~10min。
?。? 球化与孕育
(1)球化处理温度(1480±10)℃。
?。?)球化处理采用堤坝包内冲入法。球化剂加入量1.3%~1.6%。 采用钇基重稀土、珠光体球化剂与铁素体球化剂各1/3。
?。?)孕育的实质是脱氧、脱硫,形成外来晶粒,其目的是增加石墨形核能力,细化晶粒,增加石墨球数量,增加铁素体含量。
厚大球墨铸铁铸件的孕育量和孕育方式与一般薄壁球墨铸铁铸件有较大差别,对厚大球墨铸铁铸件孕育的成败起着致为关键的作用。
厚大球墨铸铁铸件因为浇注、凝固时间长,冷却速度慢,衰退倾向大,因而更应对其强化孕育。经过多次孕育,尤其是浇注过程中采用0.1%粒度为0.3~1mm的硫氧孕育剂进行瞬时孕育,效果显著。
一般球墨铸铁件的孕育量在0.3%~0.6%,但对厚大球墨铸铁件的孕育量常在0.7%~1.0%。
孕育温度(1360~1410℃,总孕育量控制在0.70%~1.20%。
强化孕育是消除厚大球墨铸铁件产生球化衰退、石墨漂浮、碎块状石墨及反白口的有效办法。
?。?浇注要求
采用低温快浇,浇注温度为(1320±10)℃。如铸件最大壁厚超过400mm,浇注温度取下限。浇注速度(15t浇包)80~100s。
最终测试各项数据(见表2、表3、表4)都获得了满意的结果。
总之,对于大断面球墨铸铁遵照以上原则,采用三步处理法;即预处理、球化处理和孕育处理,严格配料、严格管理是制造优质合格铸件的关键。
?。?铸造工艺方案设计
?。?)工艺方案分析 该件平均壁厚40mm,最大壁厚300mm。附图所示Ⅰ处长284mm、壁厚200mm,Ⅱ、Ⅲ处出气孔φ100mm,内腔芯体积约1m3。
工艺难点:①由于Ⅰ、Ⅳ两处结构对总体变形量的影响,故而控制总体反变形量较困难。②Ⅱ、Ⅲ两处出气困难。③导轨厚度较大,还需保证加工后的导轨硬度。
为此在工艺设计时,考虑到Ⅰ、Ⅳ两处对整体变形量的影响,取反变形量时,在以往经验的基础上取上限并适量有所增加,并做拉筋A 共5道。为保证导轨加工后的硬度要求,造型时在导轨面铺80mm厚石墨冷铁,同时分散内浇道。沿长度方向两侧布置内浇道φ30mm陶瓷管60道,按半封闭式浇注系统设计横浇道和直浇道。
Ⅱ、Ⅲ两处内腔体积较大,并且出气只有图示侧面这两个圆孔,为保证气道通畅,在浇注专用芯骨时预埋φ10mm吹氧管,造型时通过此管用通气绳将内腔和芯头直接联通,造型时再预埋出气绳引气。
?。?) 压箱力的计算 抬箱力先按经验估算,取4倍铸件重量约350t,再
按压强公式精确核算,得出压箱重量为278.2t,考虑到此件结构并非是抬箱力很大的类型,再加上盖箱本身的重量,因此在盖箱上压280t的压铁即可。
结语
此件清产后,总体平直度良好,导轨面最大弯曲量为7mm,完全在加工范围内。现已精加工完成,完全达到图样设计要求。
附件下载:

-
地址:济南市解放路134号 电话:0531-86401781 / 86952422 传真:0531-86465075
邮箱:foundry-shandong@163.com 邮编:250013
版权所有 © 山东省铸造协会 鲁ICP备2021002429号
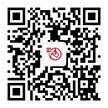
官方公众号