会员登录
MEMBER LOGIN
技术论坛
TECHNOLOGY FORUM
【铸造资料】铸态高强度高韧性球墨铸铁的关键技术
发布时间:
2015-11-14 00:00
来源:
摘要
简要总结了生产铸态高强度高韧性球墨铸铁QT590-10材质的控制要点。在合理设计化学成分的基础上,加入0.2%~0.3%Cu和0.02%~0.03%Sn可以使铸态球墨铸铁的珠光体达到70%。选择合适的球化剂和孕育剂,控制处理工艺以强化球化和孕育效果,使产品不经热处理能达到QT590-10的要求。
关键字:
铸态QT590-10、珠光体、化学成分、球化处理、孕育处理
随着对合金强化基体组织认识的加深,以及当前市场对铸件供货周期的缩短,不经热处理,减少中间环节,生产铸态珠光体球墨铸铁件已是很多铸造企业优先考虑的生产工艺。我公司生产的QT590-10材质球墨铸铁,用于汽车零配件的若干中小铸件。生产中利用合金成分及工艺控制,不进行后续热处理而直接生产获得铸态珠光体球墨铸铁,铸态珠光体达70%,生产效率高,工艺方法简单,便于操作。性能检测表明其力学性能及加工性能可稳定达到产品质量技术要求。根据本公司对生产实践的体会和总结,本文主要介绍QT590-10球墨铸铁材质生产中成分控制及处理工艺要点,以供同行在生产实践中参考。
1、化学成分的选择
?。?)碳 碳能够促进镁的吸收,改善球化、提高石墨球的圆整度;提高铁液的流动性,减少铸件的缩松缺陷和缩凹倾向;能够促进石墨化,减小白口倾向;但是,过高的碳又容易产生石墨漂浮,使铸件综合性能降低。因此将碳控制在3.5%~3.7%。
?。?)硅 铸态珠光体球墨铸铁的生产中,通常将Si控制在2.0%~2.5%,而为了在保证抗拉强度达到590MPa的基础上,伸长率达到10%,必须适当提高孕育效果,增加并细化石墨球。综合考虑,实际生产中将硅含量控制在2.5%~2.7%。
?。?)锰 锰是稳定珠光体的元素,可以提高球墨铸铁的强度和硬度。但锰降低塑性和韧性,且易产生偏析,锰量过多,易在共晶团边界形成化合物,降低铸件的力学性能,对厚大铸件更为严重。因此我公司不采用锰作为铸态形成珠光体的元素,将锰含量控制为<0.5%。
?。?)硫 硫与镁、稀土亲和力很强,消耗铁液中的球化元素,形成MgS、RES渣,降低球化率;硫越高、消耗球化剂越多,因此铁液含硫量高是造成球化元素残留量少而导致球化不良的主要原因;另外,含硫量高还容易产生夹渣、皮下气孔、热裂纹等缺陷。故硫含量控制为<0.03%。
(5)磷 磷在球铁中溶解度很低,当磷超过某一含量时,易偏析于共晶团边界形成磷共晶,降低铸件的塑性、韧性和强度,并且使铸件产生冷裂。因此磷含量控制为<0.06%。
?。?)镁和稀土 铁液中有一定的镁和稀土元素的残留量才能保证石墨成球。在稀土镁球铁中,镁起主要球化作用,稀土起辅助球化作用,并起到净化铁液、抗球化干扰元素的作用。将它们控制在如下范围:0.030%~0.05%Mg残、0.030%~0.05%RE残。
?。?)铜和锡 在共晶转变时,铜+锡促进石墨化,可减少或消除游离渗碳体的形成;共析阶段促进并细化珠光体,强化基体组织,提高基体力学性能。铸态球墨铸铁生产中,以适量的铜进行合金化是控制珠光体数量的有效措施之一,考虑QT590—10材质的力学性能对基体的要求,将铜量控制在小于0.4%范围;有限的微量合金元素锡可以使石墨球圆整度提高,增加石墨球数量,加0.03%左右的锡,可使基体组织中的珠光体数量明显增加。因此,在较高Si含量的情况下,合金化的合理设计为:0.2%~0.3%Cu+0.02%~0.03%Sn,可以有效保证铸件在铸态时珠光体达到70%以上。
2、铁液的熔炼
生产中采用3t中频感应电炉熔炼工艺,使用尽可能纯净的生铁,生铁中P、S、干扰球化元素及各类合金元素要尽可能低,回炉铁及废钢应尽可能干净,无砂、铁锈等杂物,以满足对微量杂质的控制要求。铜、锡是产品性能是否能达到要求的关键,在不利用特殊专用球化剂、孕育剂的情况下,如何确保合金在铁液中均匀,是产品质量和性能稳定的基础,考虑到两种合金在熔炼过程中不烧损,在熔炼前期以合金形式加入到炉底熔炼,可以确保合金在整炉铁液中的浓度最大限度的均匀。原铁液化学成分控制原则:在控制CE、C含量高,Si、Mn、P、S、Ti含量低的前提下,炉料配比3.6%~3.8%C,1.3%~1.7%Si。
3、球化及孕育处理
3.1球化剂的选用
球化剂的选用与铁液质量有关,原铁液中含硫量不同,选用含稀土量不同的球化剂,即使是用电炉熔炼,如果使用的生铁中含硫及其他杂质元素多,原铁液含S>0.03%,则选用SiMg8RE7的球化剂;含S<0.03%时,则选用低稀土的FeSiMg8RE5球化剂。
球化剂质量不仅与化学成分有关,而且与粒度也有一定的关系。粒度过大,不易快速溶解,使反应熔化时间长,导致球化剂上浮至铁液表面烧损,镁的吸收率下降,影响球化效果;球化剂粒度过小,特别是呈粉末状的比例要严格控制,因为铁液温度高,容易直接烧损,温度低则直接氧化[1]。生产过程中球化剂粒度的选取主要还是取决于球化包的大小和球化温度,本公司生产过程中使用300kg球化包,球化处理温度1510~1540℃,因此球化剂粒度选用5~20mm,粒度超标的球化剂应小于5%。
3.2球化处理
本公司采用通用的堤坝式冲入法球化处理,凹坑深度为100~200mm。球化前利用球铁铁屑和孕育剂覆盖球化剂,由此可提高镁的回收率15%~20%,加入量根据铁液温度决定,一般为铁液重量的1.1%~1.5%,球化反应时间一般为100~120s,球化时铁液应避免直接冲到球化剂上,球化方式应是铁液大约到1/3时开始球化反应。由于电炉熔炼的铁液纯度高、渣相少,铁液容易氧化,因此球化反应结束后,要立即加集渣剂覆盖,及时转包孕育。球化、孕育处理后的铁液应该尽可能快的浇注完毕,避免球化衰退和温度降低过多,影响产品质量。一般根据铸件大小来确定等待浇注的时间,小件不超过6min,较大件不超过15min。
3.3孕育处理
孕育剂选用常用的75FeSi,为提高孕育效果,并合理控制终硅量,根据生产条件,采用二次孕育处理方式。采用冲入法球化时在球化剂表面加入0.4%~0.5%的孕育剂,孕育剂粒度3~8mm,待冲入铁液进行球化处理时,同时发生孕育作用。在浇注前将铁液从球化包转入浇注包时,在铁液表面加入0.2%~0.3%的粒度为2~5mm的孕育剂进行二次孕育,可以有效防止孕育衰退,保障孕育效果。由于铸态QT590-10铸件的珠光体组织主要依靠合金铜+锡达到,适当加强孕育效果,有利于铸件在保证抗拉强度达到590MPa的前提下,使塑性伸长率>10%,并能有效消除碳化物,有利于铁液补缩,减小铁液收缩倾向,防止铸件产生缩松。
4、生产及检测结果
以上述方法分别测试了3炉铁液,其浇注试样的化学成分如表1所示,金相组织及力学性能如表2所示。表3是QT590-10材质要求的铁液化学成分。
表1 试样的化学成分
由表1-3可以看出,用这种工艺生产的铸态高强度高韧性球墨铸铁QT590-10的化学成分满足QT590-10材质要求的化学成分,不经热处理,其珠光体含量达到70%以上,抗拉强度达到600MPa以上,伸长率≥10%,达到了QT590-10材质要求的力学性能。
表2 球化后试样的金相组织及力学性能
表3 QT590-10要求的化学成分
附件下载:

-
地址:济南市解放路134号 电话:0531-86401781 / 86952422 传真:0531-86465075
邮箱:foundry-shandong@163.com 邮编:250013
版权所有 © 山东省铸造协会 鲁ICP备2021002429号
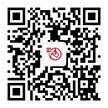
官方公众号