会员登录
MEMBER LOGIN
技术论坛
TECHNOLOGY FORUM
【铸造资料】铸钢件受力端盖的铸造工艺模拟及改进
发布时间:
2015-11-03 00:00
来源:
本文运用传统的铸造工艺设计方法对铸钢件受力端盖的铸造工艺进行了初步设计,利用View Cast模拟软件对受力端盖的凝固过程进行了模拟。模拟结果显示,在受力端盖壁厚大处会产生缩孔缩松缺陷。通过增加冒口尺寸和改变分型面位置的方法,最大程度地消除了铸造缺陷,从而获得了合理的铸造工艺方案。
关键词:铸造工艺设计;凝固过程;数值模拟
传统的铸造工艺设计建立在试错法的基础上,其缺点是试制周期长,生产成本高,质量难以控制。铸造模拟软件的应用可以大大缩短工艺试制周期,确保铸件质量,提高工艺出品率,降低成本,提高企业竞争力。铸造模拟软件V-Cast能够对铸件的凝固过程进行模拟,直观反映出凝固过程中温度场和热节部位,并能预测凝固中产生的缺陷。本文首先采用传统的工艺设计方法确定铸钢件受力端盖的基本工艺方案,再通过V-Cast软件对原工艺进行模拟计算,根据计算结果提出改进措施,优化了工艺。
1、初始铸造工艺设计
1.1铸造工艺方案的确定
受力端盖零件的三维实体见图1,根据该零件的结构特点,对该受力端盖铸件进行铸造工艺分析可知:该受力端盖铸钢件属于壁厚分布不太均匀的中型铸钢件,确定受力端盖铸造方法为砂型铸造,选用水玻璃自硬砂。
根据零件尺寸轮廓大小,确定为两箱造型,一箱一件,浇注位置选用中注式,两个内浇道,其分型面和浇注位置如图2所示。
图1 铸件三维实体模型
图2铸件的浇注位置及分型面
1.2 浇注系统的设计
铸钢的特点是熔点高,流动性差,收缩大,易氧化,故其浇注系统要求结构简单,横截面尺寸应较大,要求快速、平稳地充型,并应有利于铸件的顺序凝固。但对不同类型的铸钢,液面上升速度有不同的要求??悸堑街某叽绲拇笮『蜕浚岷现峁辜吧杓圃?,采用转包浇注,半开放式浇注系统。
浇注系统截面比为F內:F橫:F直=1.0:(0.8-0.9):(1.1-1.2),根据比例计算F內为18.4cm2,F橫为16.5cm2,F直为11.6cm2。
1.3 冒口的设计
根据模数法计算出铸件热节位置,确定在两个教大法兰的上部各采用一个圆柱形冒口,一冒口尺寸是Ф200mm×200mm,另一冒口尺寸是Ф250mm×250mm。
2、初始方案模拟
2.1 参数设定和网格剖分
用Pro/E软件绘出铸件的实体模型,转化为STL格式文件,导入V-Cast模拟软件进行实体网格划分,网格数1500000,铸钢牌号SC410(ZG55),水玻璃砂造型,浇注温度1580℃,铸型初始温度25℃。
2.2 凝固过程模拟结果及分析
根据所设定的条件和具体参数,应用V-Cast软件对铸件的凝固过程进行数值模拟,图3是铸钢件受力端盖在凝固过程中具有典型意义的几个阶段,图中透明部分表示铸件完全凝固。
当凝固时间t=250s时,型腔内金属液的边缘部分已经凝固,见图3(a);t=500s时,壁厚相对较小的部分已经完全凝固,见图3(b);t=750s时,铸件一端较小的法兰已经完全凝固,浇注系统完全凝固,见图3(c);t=1000s时,较小的冒口处没有凝固,形成孤立液相区,而较大的冒口处没有凝固,能够对铸件继续补缩,见图3(d);t=1250s时,较小的冒口处仅剩下很小的液相区,大冒口和下面的法兰之间的补缩通道减小,铸件没有形成正的温度梯度,不能形成顺序凝固,见图3(e);t=1500s时,冒口颈首先凝固,造成冒口和铸件之间的补缩通道中断,铸件内存在孤立的液相区,必然形成缩孔和缩松,见图3(f);t=1750s时,整个铸件基本上已经凝固,冒口和铸件内最后凝固的孤立的液相部分必然产生缺陷,见图3(g);t=2000s时,铸件完全凝固,见图3(h)。
(a) t=250s (b) t=500s
(c) t=750s (d) t=1000s
(e) t=1250s (f) t=1500s
(g) t=1750s (h) t=2000s
图3 铸件的凝固过程的数值模拟结果
图4为铸件完全凝固后的缺陷分布情况(金属含量低于95%时即认为是缺陷),由以上凝固过程的分析可知,整个铸件在凝固的后期没有形成正的温度梯度,缺陷主要是两冒口对法兰的补缩不够,补缩通道过早中断造成的。
图4 初始工艺缩孔、缩松的分布
3、工艺方案优化及模拟
3.1 工艺方案优化
优化方案针对初始工艺方案的不足,对其进行改进:首先是改变分型面,把具有较大热节的厚壁放到上部,其次是把冒口的尺寸加大,如图5所示
图5 优化方案三维造型示意图
3.2 优化方案模拟结果及分析
工艺改进后模拟结果如图6所示。
当凝固时间t=400s时,横浇道和内浇道以及铸件的边缘部分已经凝固,见图6(a);t=800s时,铸件小法兰的下部已经完全凝固,大法兰进一步凝固,见图6(b);t=1200s时,小法兰大部分已经凝固,冒口部分最后形成孤立的液相区,能够有效的补缩铸件,见图6(c);t=1600s时,大法兰的下部已经凝固,其冒口的温度最高,形成正的温度梯度,有利于顺序凝固,见图6(d);t=2000s时,铸件的液相区均存在于冒口之内,补缩通道畅通,能够向下补缩,见图6(e);t=2400s时,小冒口最后凝固完成,形成了正向的温度梯度,大冒口内的液相区进一步缩小,见图6(f);从t=2800s直到t=3200s之间,孤立液相区一直存在于大的冒口内,使热节完全转移到了冒口内,冒口最后凝固,实现了对铸件的良好补足,见图6(g)和6(h)。
(a) t=400s (b) t=800s
(c) t=1200s (d) t=1600s
(e) t=2000s (f) t=2400s
(g) t=2800s (h) t=3200s
图6 优化工艺模拟结果
铸件缺陷分布情况如图7所示。
铸件大法兰和环形凸起厚大部位在凝固过程中还是出现了微小的孤立液相区,凝固结束时会产生零星的缩松,但不会影响铸件的使用性能,为了消除此处的热节效应,造型时可以在此处设置蓄热系数大、易导热的铬铁矿砂,使其与相连部位同时凝固。该工艺理论上可以完全消除缩孔、缩松等缺陷。
图7 优化工艺缩孔、缩松分布
4 结论
?。?)使用V-Cast 软件对初始工艺进行了优化,优化后的工艺系统是在原工艺的基础上的改进,重新设置分型面,增加冒口尺寸,从而实现了铸件的顺序凝固。
?。?)实践表明,应用V-Cast 软件模拟铸件凝固过程,可以准确地预测缺陷类型、大小及位置,为优化工艺设计提供了可靠的依据,缩短了产品生产周期。
附件下载:

-
地址:济南市解放路134号 电话:0531-86401781 / 86952422 传真:0531-86465075
邮箱:foundry-shandong@163.com 邮编:250013
版权所有 © 山东省铸造协会 鲁ICP备2021002429号
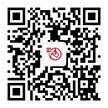
官方公众号