会员登录
MEMBER LOGIN
技术论坛
TECHNOLOGY FORUM
消失模铸造在大型箱体生产上的应用
发布时间:
2015-10-15 00:00
来源:
用消失模铸造工艺生产各种箱(壳)体类灰铁铸件,得到越来越多的应用。一般来说,箱体类铸件,特别是具有复杂内腔的各种箱体,模型不易分型、造型困难、需要使用大量的砂芯。[1] 消失模铸造工艺则可很好解决这些问题,充分体现出消失模铸造工艺的优越性和经济效益。 但是,用消失模铸造工艺用来生产箱体铸件,应该充分了解消失模铸造工艺的特点,解决消失模铸造工艺所特有缺点。这些方面主要有消失模铸造工艺使用的聚苯乙稀塑料白模,密度?。?.020~0.026g∕㎝3)、强度低,在制作、运输、组装、施涂、烘干、造型时很容易产生变形、开裂、损坏;在浇注过程中聚苯乙稀塑料白模的裂解产物也容易残留在铸件中形成缺陷。对于大型复杂壳体类铸件,由于白模的尺寸和表面积较大,在上涂料时和埋箱振实时,受到的涂料的浮力和型砂的作用力很大, 极易变形和损坏;较大体积的白模,浇注过程也将产生较多的裂解产物,铸件形成夹渣类缺陷倾向大。这些都是消失模铸造工艺是不可避免的的现象,因此必须根据铸件的结构特点,制定组装、涂挂、烘干、加砂、振实造型工艺和采取合适的白模加固措施。 我们的产品后传动箱体就是这样一类大型复杂箱体类铸件,要应用消失模铸造工艺来生产就必须根据零件的具体结构特点,选取合适的工艺参数和采取必要的措施。
1 产品概述
后传动箱是一种结构形状复杂,尺寸、重量较大的零件,它复合了多个零件在一起,材质牌号HT250。它由四个相通的型腔和一个独立的型腔组成,内部及及外表面许多部位都有很严格的尺寸及形位公差。主要壁厚为15mm,局部厚处80mm,外形尺寸1050×925×750(㎜)。由于该铸件结构复杂及尺寸重量较大,内腔各腔体之间连通部分较小,制作整体砂芯困难,铸件四周均有上下法兰,需要一周砂芯,不易在我公司现有的造型线上流水生产,原生产工艺采用自硬砂手工造型生产。为了实现它复杂的内腔和外型结构,需要作出十六个砂芯,而且有些部位砂芯套砂芯,造型操作十分复杂困难,每箱铸件要耗费数吨树脂砂。这种工艺生产出来的铸件,外表粗糙,尺寸精度低,每个铸件重660Kg左右。
2 消失模铸造工艺工艺参数选定
2.1白模 白模材料采用普通的EPS发泡成型。 根据保证模样尺寸精度与刚性,减少多次拼接造成误差和变形的原则,后传动箱的 白模分为四片制出,用冷胶粘组装结成形。
考虑到铸件尺寸较大,在上涂料和造型时将会承受到较大的作用力,白模材料密度取较大一些,为0.023 - 0.026 g/cm3。 浇注系统选用合适的泡沫塑料(EPS)板材,用电热切割的方法制作,以后与模样粘结。
2.2模样放置与浇注方案确定 消失??刹捎玫鬃?、侧注、顶注、阶梯式注等浇口设置方式。根据模样在砂箱中不同的摆放位置又可采用不同的浇注方案,他们都有各自的特点。浇注系统的设置要考虑到模样在砂箱中的摆放,便于填砂紧实,铁水充型合理。我们根据铸件的结构特点和生产经验,分别设计了几种浇注系统方案,应用计算机数字技术,进行铸件的模拟凝固和模拟充型过程分析,帮助我们进行工艺设计优化。
参考计算机模拟凝固、充型的结果和原手工造型工艺方案,本着方便金属液充型和热解产物顺利排出,有利于铸件补缩,防止铸型溃散塌箱及粘砂、变型等缺陷,有利于造型时填充型砂,我们对原设计的浇注系统方案进行完善优化,最终决定采用有较大开口向上的铸件卧式放置的侧浇方案。横浇道围绕着铸件的二个侧面分布,直浇道设在横浇道的拐角处,内浇道在横浇道的两条边上根据箱体的结构各设置三个(见图3)。直浇道:横浇道:内浇道=1.4:2:
为了减少铸件的夹渣、绉皮、积炭等缺陷,在模样顶部及某些端部设置一些出气集渣小冒口片。
2.3涂料及施涂方法的选择 消失模铸造涂料用浸涂法施涂,有生产效率高,节省涂料、涂层均匀等优点。但由于泡沫模样密度小(与涂料密度相差几十倍),且本身强度又很低,浸涂时浮力大,因此仅适用于模样可浸入或半浸入涂料中的中小件和壁厚件。 后传动箱的泡沫塑料模样,经测算,它在涂料液中产生的浮力超过120㎏,人力是完全不可能把它浸入涂料中去的。它是一个尺寸较大的空腔壳体,十分容易在一些受力部位产生变形和断裂。对这类模样,只能用喷淋、刷涂的方法施涂。为此,我们设计制造了一台专用涂料喷淋装置,使涂料可源源不断的从管口流出,具有喷淋功能。上涂料时,通过翻转模样,可将涂料喷淋到里里外外各个部位。 涂料使用我们自已研制的水基铝钒土涂料。 涂层厚度控制在1.2mm左右。 考虑到模样在施涂过程中需不断的翻转,而且要多人合作完成,浇注系统容易碰掉或损坏。因此,我们把模样及浇注系统分开上涂料,烘干后再组装起来,并进行必要的修补、烘干。 模样的烘干温度为50℃±5℃。
2.4造型工艺 砂箱的负压抽气方式我们采用的是底抽和侧抽相结合的方式 干砂选用内蒙产石英砂,粒度为30/50目,其主要化学成分见表1。
由于雨淋式加砂有利于干砂的均匀加入,可以避免对模型造成强烈的冲刷和撞击,损坏模样和涂料层。因此加砂方式采用雨淋式加砂为主,辅助以柔性加砂管。 振实由可变频的三维振实台来完成。
2.5熔化和浇注 根据图纸要求,铁水熔炼和炉前处理工艺完全按HT250材质控制??悸堑较V旃ひ罩诟缮爸欣淙唇下?,铸件本体的硬度和强度比普通砂型铸造低,我们对铁水做适当合金化。 对消失模铸造来说,由于泡沫模样的存在,浇注过程中会消耗一定的热量,因此消失模铸造的浇注温度一般应比普通砂型铸造要高一些。铸件复杂程度不同、壁厚不同,浇注温度也应不同。由于后传动箱较大,也不属于薄壁类铸件,它的热容量大,对型砂的热作用时间长。浇注温度太高,在负压的作用下,在铁水凝固过程中铁水穿过涂料层,渗入型砂中,并粘附在铸件表面,形成粘砂现象。我们根据后传动箱的结构特点,浇注温度确定控制在1380℃~1430℃[2]。浇注时保证直浇道始终处于充满的状态. 始浇真空度选择0.04 MPa~0.05 MPa,并控制在浇注过程中真空度不低于0.02 MPa。 根据经验及资料推荐,每个铸件的浇注时间控制在40秒~50秒。
3 生产应用结果 调试及其生产在我所年产1000吨铸件的小型消失模生产线上进行。 根据上面所选的工艺参数,解决试制中出现的问题,最终生产出合格的消失模铸造工艺后传动箱铸件。用消失模铸造工艺生产后传动箱铸件,每个箱体重615Kg,不但简便了造型方法,节省大量的树脂砂,而且外观清晰,尺寸精度高,充分体现了消失模铸造工艺的优势。 结果表明,我们选定的工艺方案基本是可行的。 生产过程中抽查检测,部分铁水化学成分及Φ30单铸试棒的机械性能见表2。
灰铁铁的冷却条件不同,使同一铁水浇注的标准试棒和铸件本体的性能有一定的差别[3]。我们对上表序号1的铸件进行了铸件本体检测。铸件本体取样的部位为箱体端部,厚度35mm左右,结果如表3。
4 应用体会 经过试制及生产,我们对用消失模铸造工艺生产大型复杂箱体类铸件有如下的看法: 因为模样在涂料液中的浮力太大,上涂料时手持的部位或其他较薄弱的地方很容易损坏,对于尺寸较大的空腔类铸件,上涂料用浸涂的方法不宜实现。对这种大型空壳类零件,淋涂法是较适宜的工艺方法。浸涂或半浸涂一件白模,仅需几秒钟时间,而对大型复杂件上涂料,需要数分钟时间。因此,上第二遍及其更多遍涂料时,应尽减少涂料液与模样的作用时间,因为时间长了,上一层涂料会彻底润湿,很容易与第二遍涂挂上的涂料层一起从模样上脱落下来。 填砂造型遇到水平面结构时,如箱体内的分腔隔板,要注意先将其下底面填满振实,再往上面填砂。若在水平面底部没有紧实的情况下在其上面加砂及振实,会造成水平面随着上面堆积的型砂下沉而变形。其他易发生变形的水平部位(如悬壁结构)也应在易变形部位牢固后再继续加砂振实。我们在生产过程中,就出现过箱体水平面
部分随型砂下落而变形的情况。在模样的腔体部位,应保证腔体内外所加的型砂大致平衡,避免模样在振实过程被砂流挤压发生外凸或内凹变形的现象。 形成箱体内腔的铸型砂块与其他部位联接的截面若太小,浇注过程中铁水产生的浮力大于联接截面的强度时,将会使箱体内腔砂块在联接处断裂而上浮或移动,造成铸件上面壁厚减薄或穿透形成与内腔形状相同的透孔,而下面壁厚增加。这种现象和普通砂型铸造中砂芯断裂的表现和原理一样。解决的办法有:适当增加真空度,以加强联接截面的抗拉或抗剪能力;在易断裂处插入金属加强筋,也就是相当于砂芯的芯 骨,加强此处的抗破坏能力。在浇注过程中要注意观察砂箱内的负压状 况,真空度不要出现太大的波动。出现真空度突然剧下降时,要适时进行调整。图6所示即是由于形成内腔的砂块断裂上浮移位,造成铸件空腔上移至表面形成穿孔。我们试制时没有采取措前每件都有相同缺陷,而使用加强板后这种现象再也没有发生。 大型壳体类铸件在造型时,由于表面积较大,型腔内外受到型砂的作用力很大,而泡沫塑料模样的强度很低,极易变形。因此应根据每一种铸件的结构特点,制定加砂、振实造型工艺和采取合适的加固措施。 用消失模铸造工艺生产结构复杂和尺寸较大的箱体铸件,由于铸型刚度在负压的作用下很高,退让性不好,铸件在凝固过程受到的应力十分复杂,对铸件的收缩特别有影响,有自己独有的特性,会发生铸件有的部位没有缩尺,而有的部位缩尺正常的现象。
生产小型、简单、厚实的铸件时不受注意的缩尺,在生产大型的空腔件就可能构成问题。我们生产的箱体铸件,缩尺最大放有8mm以上,这样的误差就有可能造成铸件报废。因此,在铸造工艺设计时,应根据铸件的结构及尺寸情况,考虑自由收缩和受阻收缩,确定铸件不同部位有合适的缩尺。
附件下载:

-
地址:济南市解放路134号 电话:0531-86401781 / 86952422 传真:0531-86465075
邮箱:foundry-shandong@163.com 邮编:250013
版权所有 © 山东省铸造协会 鲁ICP备2021002429号
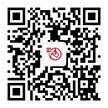
官方公众号