会员登录
MEMBER LOGIN
技术论坛
TECHNOLOGY FORUM
湿型砂的配方怎么定?
发布时间:
2015-01-09 00:00
来源:
一.前言
要想生产出优良品质的湿砂型铸件,必须使用优秀性能的湿型砂。湿型砂性能的获得,除了要使用优质的原材料和良好的混制工艺以外,还需要有一个合理的配方。同一种造型方法、同一种类型铸件和同样的品质要求,国内外的湿型砂性能要求是基本类似的,可以互相参考借鉴。例如国内外稳定生产中小灰铸铁件单一砂的型砂性能都基本上符合下表所示。各项性能都是从造型处取样的测定结果。含泥量是指型砂而言;有效膨润土量是指5.00g型砂用0.20%浓度试剂纯亚甲基蓝溶液的滴定量[mL];有效煤粉量是指1.00g 型砂900℃的发气量[mL]。性能的波动范围根据铸件大小、厚薄和结构、以及清理方法不同而异,一般情况可取中间值。
至于混砂配方的确定则各工厂可能有较大出入。铸铁湿型砂批料配方的最主要组成物 是旧砂,此外还补充加入原砂、水、膨润土、煤粉。在生产中旧砂和新砂加入量的比例并不经常变化,通常将旧砂和新砂量之和做为100%。膨润土、煤粉和水的加入量可能随时调整,因此将这三种材料加入量按超过100%计算。下表为某些工厂生产中等大小灰铸铁件的单一砂批料配方的例子。原材料为内蒙砂、优质膨润土、优质煤粉;砂铁比5~7;落砂时树脂砂芯混入旧砂中约占旧砂量的0.5~2%;无旧砂除尘冷却装置;铸件经抛丸清理。型砂干湿程度根据手捏的感觉或紧实率检测值,含水量为参考值。
但是国内很多工厂的批料配方与表中数值相差很多,例如铸造手册(造型材料第2 版)第103~104页的表格中列举了国內9家著名大型铸造工厂的铸铁单一湿型砂。膨润土加入量有的为2~4%,还有极个别的高达5%。煤粉加入量有的为0.75~2%,也有的高达3~4%。至于民营中小铸造工厂的批料加入量可能有更大差异?;焐凹铀咳【鲇谛蜕暗母墒潭取2⒉桓鼍咛寮尤肓?。
以下将讨论其他几种批料的加入量是如何确定的。
二.膨润土的批料加入量
在生产中都是根据型砂试样的湿压强度来确定膨润土加入量是否足够。补加膨润土的目的是补充膨润土被烧损的损失,另一方面,新加入材料如新砂、混入芯砂和煤粉也需要靠加入膨润土进行黏结使具有足够强度。
1. 膨润土的烧损量
膨润土晶体受热造成一定程度破坏,再加水混合后湿态黏结力将明显下降。更高温度和更长时间加热后,膨润土的晶体结构完全破坏,就变成没有黏结力的“死黏土”。对比型砂和旧砂的有效膨润土量可以得出膨润土的烧损量。天然钠基膨润土热稳定性高于钙土,用碳酸钠活化处理过的钙基膨润土热稳定性明显提高。例如某外资铸造工厂的挤压造型线原来使用进口天然钠基膨润土,混砂批料配方中膨润土加入量长期以来都是0.9%。后来改用一种国产活化膨润土,刚开始时也加入0.9%即可达到所要求的强度。但是经过砂系统几次循环后,发现加入量必须提高到1.0%才能恢复所要求强度。其原因就是两种膨润土的热稳定性不同。膨润土本身粘结力高低也对烧损量有影响,如果为了达到规定的湿压强度,某种膨润土需要加入量为另一种膨润土多一倍,则烧损量比后者高一倍。型砂要求强度高而,需要多加膨润土,烧损量也会增多。铸件厚度增大,砂/铁比(S/M)低,浇注温度高和冷却时间长都都使膨润土的烧损量增多。
2. 新加入材料的膨润土补充量
混砂批料配方中新加入的原砂和煤粉、混入旧砂中的溃散芯砂都需要额外补充加入膨润土来粘结才能达到同样的有效膨润土量。例如某一湿型铸铁工厂的单一砂要求有效膨润土量8%。砂芯混入量很少,可以不计?;焐芭系脑凹尤肓?0%,煤粉加入量0.5%。为了将新加入原砂和煤粉黏结产生足够的型砂强度,也达到含有效膨润土8%,需要补充加入膨润土量为:8%×(10+0.5)% = 0.84%。
混砂时膨润土总加入量是烧损量与额外补充量之总和。
三.煤粉的批料加入量
判断型砂中有效煤粉是否足够的最直接方法是观察铸件表面的光洁程度和有无粘砂。受到浇入金属液热作用,旧砂中一部分煤被烧损,需要补充。另一方面,新加入材料如新砂、混入芯砂和膨润土也需要靠加入煤粉使达到有效煤粉量的水平。
煤粉的品质是影响煤粉的烧损的一个重要因素,例如某厂的湿型砂中有效煤粉量4%已然足够,而使用另一种煤粉需要有效量6%才能达到同样铸件表面质量,则后者的浇注损耗量比前者多50%。另外铸件光洁度要求高低不同、厚薄不同都要求不同的有效煤粉量,浇注的烧损也必然不同。我国大多数铸造单位都是用发气量测定仪来检测铸铁用湿型砂中有效煤粉量。检查型砂在浇注前后的有效煤粉量变化就可以得出煤粉的烧损率。
混砂批料中新加入的原砂(包括溃散芯砂)和膨润土都需要额外补充加入煤粉来达到同样的有效煤粉量。例如某一湿型铸铁件工厂的单一砂要求有效煤粉量4%。砂芯混入量很少,可以不计?;焐芭系脑凹尤肓?0%,膨润土加入量1.0%。为了使将新加入原砂也具有4.0%有效煤粉量,需额外补充加入煤粉量为:
4%×(10+1)% = 0.44%。
混砂时煤粉总加入量是烧损量与额外补充量之总和。
国内外一般铸造工厂通行的办法是根据材料品质不同,将煤粉加入量与膨润土加入量规定成一定比例,使煤粉的加入量随膨润土的补加量而定。例如有些工厂的优质和高效煤粉补加量是优良品质膨润土补加量的1/2.5~1/3。
四.原砂的批料加入量
一般情况下,混制单一砂时原砂加入量只不过占批料总砂量的0~10%。
1. 加入原砂的目的
在铸造过程中,型砂中的砂粒会或多或少地丢失。有些砂粒在混砂和浇注过程中受到机械应力和热应力破碎成为微细颗粒和粉尘而被除尘系统排除。铸件较厚大,浇注温度高,铸铁型砂中煤粉含量少,有一些型砂粘附在铸件表面上被带往清理工部成为废砂。高密度造型的型砂强度和砂型紧实程度高,砂型边缘和角落没受到金属液加热处最不容易破碎开,就会形成大砂块。再加上落砂和过筛设备的破碎效果差,砂块会随铸件跑掉或被筛掉。因而必须添加原砂以补充砂粒损失来保持砂系统的总砂量不变。另一方面混砂新加入膨润土、煤粉等材料使型砂的含泥量增多,需要靠加入原砂维持型砂含泥量不变?;髟煨偷氖蜕昂嗔恳话惚3衷?2~14%。如果泥分过高,必然提高型砂含水量,降低透气性。泥分中也包括灰分,即被烧损的死粘土和死煤粉,以及新加入的原砂、膨润土和煤粉等材料中的一些无效灰分。型砂的灰分过多使型砂韧性下降。当落砂、过筛和运送等过程中除尘设备可以去除一定量泥分和灰分。但旧砂处于潮湿状态,除尘效果有限,绝大部分粉尘仍然残留在回用砂中,混砂时加入新砂可平衡回用砂中的泥分和冲淡灰分。
2. 原砂加入量计算
首先计算出各种新加入材料在浇注后的型砂中产生多少泥分,才能计算出这些泥分需要加入多少原砂才能够使型砂含泥量符合工艺规定。以下用两个简化的例子说明批料带入的泥分总量有多少,需要用多少原砂平衡。由于测定各种材料的泥分都是使用烘干状态,而所加入材料量都是含有少量水分的材料。所以在计算新加入批料带入泥分量时需要扣除所含水分。 例一:某铸造工厂的单一型砂要求含泥量15%,只有少量砂芯,落砂时溃散砂芯混入旧砂量极少,可不计。
混砂所加原砂为未经水洗的当地砂,含泥量(即灰分)3%,含水量2%。含SiO2较低,落砂时旧砂中出现的烧结块,排除后做为废砂扔掉。新原砂加入量18%弥补砂粒损失。扣除水分后由原砂带进型砂的泥分:
3%×(100-2)% ×18%= 0.529%
加入的膨润土品质较差,吸蓝量只有25ml,含水量10%?;焐凹尤肓?%才能使型砂强度达到要求?;焐笆庇膳蛉笸两胄蜕暗哪喾郑?br />
(100-10)%×3%= 2.7%。
煤粉品质相当差,挥发分只有25%,灰分20%,含水量5%,为了防止铸件表面粘砂,混砂批料中加入煤粉2.5%。由煤粉带入型砂中的泥分:
(100-5)%×2.5%= 2.375%。
三种材料新带入泥分量合计:0.529+2.7+2.375 = 5.604%。
使新带入泥分在混好型砂中也达到含泥量15%的水平,需加入不含水、不含泥分的原砂量:
折合含泥含水原砂:37.36/(1-0.2+0.3) = 39.33%
需要原砂量已经远远超过实际加原砂量的18%。长期生产的结果是型砂中含泥量越来越多,型砂性能越来越坏,铸件废品率越来越高。
例二:另一工厂使用优质原材料,型砂要求含泥量13%。为了补充砂粒损失,原砂加入量为10%。只有少量带砂芯铸件,混入芯砂可忽略不计。各新加材料带入灰分分别如下:
原砂用内蒙水洗砂,含泥量为0.5%,含水量2%,加入量为10%,带入型砂泥分为:
0.5%×(100-2)%×10 % = 0.049%
膨润土用优质的,含水量10%,混砂加入量只需0.8%,带入泥分:
(100-10)% ×0.8% = 0. 72%
煤粉也用优质的,含水量5%,混砂加入量只需0.3%,带入型砂中泥分:
(100-5)%×0.3 % = 0.285%
三者合计带入泥分:0.049%+0.72%+0.285% = 1.054%。
为了使新增泥分达到同样的型砂含泥量13%,需要原砂(含水和泥分)冲淡量:
平衡新带入泥分只需用原砂8.32%,不超过弥补砂粒损失原砂加入量10%。能够保持型砂性能和铸件品质稳定在预期水平。
五.溃散砂芯的混入
有些铸造工厂大量应用树脂做为砂芯粘结剂,改善了溃散性能。新型落砂设备的效率提高,也增大了溃散和破碎的砂芯混入旧砂量。混入的砂芯可以代替部分或全部新砂,用来弥补型砂的损失,并可平衡型砂的泥分。此外,树脂芯砂的混入还能利用砂粒上残余的树脂膜,部分地代替铸铁湿型砂中的煤粉防止铸件表面粘砂。流入旧砂的砂芯量占旧砂量的比例因工厂的生产条件、铸件种类等众多因素而异。第一汽车公司第二铸造厂三种汽缸体铸件落砂时,一部分芯头被筛除掉,大约有砂芯重量的80%溃散流入旧砂中,占砂箱中旧砂量分别为1.96%、3.25%和4.4%。德国KHD铸造厂生产曲轴箱和汽缸头等铸件,使用冷芯盒砂芯和壳芯。以其中两种铸件为例,第一种铸件在落砂时,砂芯的90%流入旧砂中,占砂箱中旧砂量的6.7%。另一种铸件的砂芯有70%流入旧砂中,占旧砂量的16.0%。Harzer铸造厂生产汽车球铁件和灰铁件,芯砂流入量达到型砂总量的12%。砂系统不加新砂,只靠溃散芯砂流入即可满足补充砂粒损失和平衡泥分、冲淡灰分的需要。
为了估计经过长时期多次循环后,型砂中芯砂所占份额如图所示。图中加入量为砂芯混入量,计算的条件是假设旧砂的损耗量与芯砂流入量相等。由图看出随着循环次数的增多,芯砂在型砂中占有的份额逐渐增加,直到100%。如果混砂时还加入原砂,其量与砂芯混入量相同,则最终的型砂中来自原砂与来自芯砂的砂粒各占一半。旧砂中不断积累了多量溃碎砂芯,有可能给型砂性能带来多种负面影响,以及可以采取措施:
⑴ 砂粒度变粗
震压造型铸造工厂所用湿型砂的粒 度大多是70/140,高密度造型的型砂粒度应当为50/140,而树脂砂芯粒度大多是50/100或更粗些。芯砂混入过多就会影响整个湿型旧砂的粒度变粗,从而引起型砂透气性增高,铸件表面变得粗糙。为了保持型砂的粒度不致变粗,可将除尘系统的微?;厥盏骄缮爸?。必要时需要加入细粒新砂来纠正,例如美国一灰铁铸造工厂在混砂加入5%集中在100和140目的两筛分布细砂来改善型砂粒度。
?、?砂性能变差
掺入大量树脂芯砂的湿型砂韧性下降、发散、湿态强度和热湿拉强度降低。未受热烧损的芯头的伤害作用更为显著。国外有人认为需要少许延长混碾时间和增多膨润土加入量就能够抵消混入树脂芯砂的不良影响。
?、?系统容纳量不足
生产发动机气缸体的工厂得旧砂中溃散砂芯混入量可能相当大,已然超过补充砂粒损失量、以及平衡新材料带入泥分的需要量。即使混砂时不加入新砂,也不得不经常故意扔掉一些旧砂以免砂系统中总砂量过多。而所扔掉的旧砂都是品质最好的砂子。应当采取旧砂再生用于制芯,减少砂芯混砂的新砂用量。
?、?砂团块量增多
未烧损的砂芯心部及芯头,经破碎过筛后,仍有相当部分玉米粒大小砂团块进入混砂机。经过短时间混制后,还有小的芯砂团块存在型砂中。这些小团块如在砂型内部,对铸型及铸件不产生损害;如果在砂型表面,特别是在模型凹槽或棱角处;将影响该处的紧实度,引起局部疏松,有可能产生粘砂、冲砂、砂眼、轮廓不清等缺陷??梢栽銮炕焐承Ч扑榭巴?。
六.如何用全新砂混制型砂
由前可知,混砂的基本材料是旧砂。任何新建铸造工厂或新建造型线都愿从本厂、本地甚至外地找到适宜组分和性能的旧砂当做自己新安装设备调试和生产的出发点。这是因为用全新砂会出现种种困难,主要是。
1. 新砂受热膨胀量大,特别是在573℃的石英相变引起体积急剧胀大,容易引起膨胀缺陷如夹砂、鼠尾。而石英砂经过反复受浇入铁水的加热转变成方英石,冷却时并未完全恢复原来的体积,再受热时膨胀量减小。
2. 为了使混制的型砂具有工艺规定的强度和抗粘砂性能,需要加入大量膨润土和煤粉。从试制开始直到正常生产阶段为止,膨润土和煤粉加入量是逐渐变化的,必须随时花费较多精力随时监控型砂性能并不断调整加入量。
3. 全新砂的型砂含泥量低,型砂的透气性肯定较高,试浇出铸件表面粗糙甚至有粘砂。
4. 全新砂的型砂含泥量、微细砂粒量、灰分量较低。同样紧实率的水分量低,保水性差,对水的敏感性高。含水量稍微有偏差(例如±0.20%)就会引起其他各种性能波动。
5. 让大量膨润土包覆在相当光滑的新砂表面需要较长的混碾时间和较多的电能输入。否则型砂的韧性、可塑性、都会偏低。
如果新建工厂确实找不到适宜的旧砂当做混砂的基本材料时,可以采取的措施:
1. 完善工厂的型砂实验室,用来检测各种型砂原材料样品的品质和性能,从中选择较适用的和品质较优的材料。而且利用实验室的小混砂机进行试配型砂。
2. 探索配方时首先确定适宜湿态强度的膨润土加入量。
3. 如果透气性尚未超过允许极限,还可以勉强用于造型。例如要求型砂透气性80-100,在开始时透气性140以内尚可使用,但不可超过160。如果发现透气性已然过高,就需要掺加细砂调低型砂粒度。另一个办法对工厂可能更方便些,就是在型腔表面喷涂料。
4. 抗粘砂效果的检验主要靠浇注试验
5. 在开始使用大混砂机和用造型机时,应当注意到混砂需要时间可能是正常生产时的一倍以上。
七. 结论
1. 确定湿性砂配方首先要使强度符合要求,也尽量要透气性不超出是以范围。
2. 加入膨润土、煤粉的目的是补偿烧损量,以及使新加入的其他材料也达到同样的有效膨润土量和有效煤粉量。
3. 加入新砂的目的是补充砂粒损失量和保证型砂含泥量不增多。
4. 溃散芯砂流入旧砂中可以替代原砂,但须注意透气性增大、韧性降低、旧砂量超过容纳范围、型砂中出现团块。
5. 用全新砂混制型砂会出现铸件膨胀缺陷、粘砂缺陷,以及性能不适当。
附件下载:

-
地址:济南市解放路134号 电话:0531-86401781 / 86952422 传真:0531-86465075
邮箱:foundry-shandong@163.com 邮编:250013
版权所有 © 山东省铸造协会 鲁ICP备2021002429号
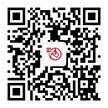
官方公众号