会员登录
MEMBER LOGIN
技术论坛
TECHNOLOGY FORUM
我国铸造磨球的生产及研发现状
发布时间:
2013-10-31 00:00
来源:
据统计国内磨球年消耗已经超过200万t,冶金矿山消耗的磨球占各行业磨球消耗总量的70%。2006年为例,磨球损耗造成的经济损失不少于40亿[1-2]。由此可见,磨球在耐磨材料中占有相当大的比重。我国目前铸造磨球的生产厂家有1 000多,但年产量大多数在3 000t以下,万吨的企业不到10家。而磨球的国内需求及出口量逐年增多,对磨球的质量要求也逐步提高:本文从铸造磨球材质的研发及磨球的生产工艺等方面介绍了铸造磨球的现状,并对铸造磨球的发展提出了观点。
一、铸造磨球
磨球按材质可分为金属磨球、非金属磨球,金属球包括钢球、铁球;非金属球包括无机非金属和有机高分子材料,其中无机非金属材料中包括氧化铝、氧化锆、硅酸铅、碳化硅、碳化钨、氮化硅等合成材料,也包括玛瑙、砾石、卵石等天然材料;有机高分子材料包括聚四氟乙烯等材料。
金属材料磨球按照制作方式又可以分成锻球、轧球和铸球[3]:其中铸造磨球的丁业应用非常广泛,我国年产达到了百余万吨。在冶金、建材、电力、化工等行业,磨球都有大量的应用。因此,与磨球相关的国家及行业标准也很多。由于目前尚无铸造磨球的国际标准,因此在最新的铸球国家标准中参考了美国ASTM和欧洲耐磨铸铁件标准[4]。新修订的国家标准《铸造磨球》与原标准比分别增加了磨球的牌号,将磨球直径分为5类,减少了铸造
磨球的直径公差,并将在国内已有生产并取得好的工业效果和性价比的磨球列入国家标准(ZQCr12、ZQCr5、ZQQTM),依据生产和应用增加了C、Si、Cr的含量范围,提高了铸球表面硬度要求(ASTM耐磨铸铁件的中上水平):标准制定水平的提高,反映了我国铸造磨球生产的技术水平有了长足的进步:下面笔者将介绍铸造磨球在我国的研发及生产现状:
二、铸造磨球的研发
2.1 计算机模拟技术在铸造磨球上的应用
计算机模拟技术,可提高产品质量、增加产品成品率、降低工程技术成本、降低人工成本、增加设备利用率、缩短产品没计周期等[5]。同样该技术也被应用于铸造磨球的生产研发
之中,Suslo N V等人利用模拟技术对ф60mm铸球生产的铸则进行模拟,将原3球铸型,改进成4球铸型,铸球的缩孔率由原来的0.5%减少到0.08%,见图1。同时也对不同材质的铸球进行了模拟,结果见图2[6]。国内也有人利用温度场数值模拟软件对金属型耐磨铸球的凝固过程进行数值计算。利用模拟结果改进铸球铸造工艺,达到消除缩孔缺陷,提高产品质量的目的。为企业节约生产成本,提高产品工艺设计效率[7-8]。
数值模拟技术在铸球生产中的应用包括以下几个方面:①改进铸型没计,包括铸型的壁厚、铸型布局等;②预测铸球可能产生缩孔等缺陷的条件,以便制定合理的工艺方案;③通过对铸球不同生产:方案的模拟,选择最优的方案进行生产,减少了企业生产试制的成本;④在特殊尺寸铸球(大尺寸)的研发中采用模拟技术,确定合理工艺,提高研究效率,减少研制成本。
2.2 提高铸造磨球性能的研究
磨球在研磨过程中分别与磨料、衬板及磨球间发生摩擦与冲击,在这过程中,磨球承受着冲击抛落时的较大冲击和碰撞时的较小冲击、法向压力、切向力及磨粒的磨削作用[9],见图3。因此,高的耐磨性与好的韧性一直是磨球生产厂家追求的目标。
2.2.1 铸造磨球的材质
磨球相关的国家及行业标准中对铸球的成分都有相关的规定,这些标准包括:GB/T17455—2009僻造磨球》、YB/T 092—2005《合金铸铁磨球》、JC/T533—2004《建材了业用铬合金铸造磨球》、DL/T68l一1999<耱煤机耐磨件技术条件》等。相应标准对铸球成分的规定分别见表l—5110-13]YB/T092—2005拾金铸铁磨球》中铬系铸铁磨球的化学成分应符合表2的规定,球墨铸铁磨球成分见表3,金属磨球可分为钢球和铁球,钢球包括
图3 球磨种磨球运动示意图碳钢球与合金钢球;铁球包括普通铸铁球、合金化铸铁球、天然多元素低合金铸铁球。钢球则主要是锻轧球为主,还包括普通铸钢磨球及新型合金化铸钢磨球;铸造磨球是以铸造铁球为主,这从卜面提及的几个国家及行业标准中就能看出。近些年我国研发的磨球材质主要有中高碳钢锻球、贝氏体锻钢球,高铬合金铸球,中铬合金铸球,低铬合金铸球,贝氏体球墨铸铁球,贝氏体、马氏体复相球铁磨球[14-15],这些磨球中铸造磨球占了相当大的比例。
2.2.2 铸钢磨球
铸钢磨球研究主要通过合金化及热处理来提高铸球的性能,即通过合金化和热处理改变铸球组织,从而提高铸球耐磨性。如徐志明等人采用高硅微合金化方法和中断正火热处理研制出的ZG55SiCrMoTiBRE铸钢磨球,其成分为:0.5%~0.6%C,0.9%~1.4%Mn,
0.7%~1.4%Si,1.0%~1.4%Cr,0.2%%~0.4%Mo及微量Ti,RE,B,还有常量的S,P,使用寿命比锻钢磨球高3倍,比ZG55铸钢磨球高1倍以上[16]。
符蓉等研究了利用铸造余热对铸造磨球进行处理,铸球中断正火后,获得了贝氏体和马氏体复合组织,对比试验中的ZG45铸钢磨球与ZG45SiMnCrMo铸钢磨球比,抗磨系数由1.5升至3.5[17]。以上研究的共同特点就是利用合金化及热处理获得贝氏体和马氏体复合组织,以期获得高性能。贝氏体是由Bain在20世纪20年代末发现的,是一种强韧性配合良好的组织,其组织的特殊性能受到广泛重视,贝氏体领域的研究工作也得到广泛开展[18],这其中就包括铸造磨球。
一般情况下随着淬火温度的提高,钢球的硬度增加,但过高硬度反而下降;淬火温度及回火温度对铸钢磨球的力学性能有着不同的影响,对于成分不同的铸钢磨球,淬火及回火温度存在一个最佳组合。
表6为几种铸钢磨球采用的热处理力·式及铸球的力学性能及金相组织[16,19-20]。从表6中可以看出,高性能铸球的金相组织基本都是贝氏体+马氏体+少量奥氏体,而最佳热处理工艺就是为了获得这二种组织的最佳配比。
2.2.3 铸铁磨球
根据GB/T17455—2009《铸造磨球》,磨球被分为铬合金铸铁磨球及球墨铸铁磨球,其中铬合金铸铁磨球根据铬含量的不同分成不同牌号,球墨铸铁磨球根据热处理后获得基体组织的不同分为贝氏体球墨铸铁磨球及马氏体球磨铸铁魔球。与铸钢魔球不同,铸铁魔球的研究主要集中在不同铬含量魔球在不同领域应用情况的研究及高性能CADI魔球的研究等方面。
不同磨机工况,如干磨、湿磨,不同矿物等,都应选择相对适合的磨球。能满足所有工况条件要求的磨球还没有,都需要结合具体的工况,对磨球材质进行优化。如王广瑞等人通过对比不同磨介材料研究,确定对于黑山铁矿,低铬钒钛铸球具有良好的耐磨性;同样王鹏等研究了低铬多元合金球在凡口铅锌矿上的应用,认为低铬多元合金球用于金属矿山湿磨工艺,比高铬球、中锰稀土镁铸球磨矿费用更低[21-22]。
低铬多合金白口铸铁球的特点是铬含量低,价格较低。大多应用在水泥、电力干磨作业,耐磨性是普碳钢球的7~8倍,应用于矿石等湿磨作业优势更明显,是低碳钢球的2.5~3倍,是中高碳钢球的1.5~2倍。
高铬与中铬多合金铸铁球由于含较高铬元素,其金相为马氏体基体上分布着不连续的碳化物,而碳化物以(Cr,Fe)7C3为主,因而其宏观硬度很高(HRC 50以上),又有一定韧性,具有优良的耐磨性。Crl2磨球,可铸态使用,只进行简单的低温去应力处理即可,组织为细珠光体组织+碳化物+残余奥氏体。其耐磨性是普碳钢球的10倍以上,大受电力、水泥行业欢迎[23]。贝氏体或马、贝体球墨铸铁磨球的金相组织,是由马氏体、贝氏体和球状石墨良好配合而成,具有良好的淬透性和硬韧性。其耐磨度为普碳钢球的2.5~3倍,价格偏贵。
2.2.4 铸造磨球显微结构的研究对铸造磨球的显微组织,GB/T17455—2009《铸造磨球》中没有具体说明,而YB/T092—2005《合金铸铁魔球》中对高、中、低铬铸铁磨球及贝氏体、马氏体铸铁磨球分别做了定义,DL/T681-1999《磨煤机耐磨件技术条件》中对球磨机磨球的金相组织和使用特性也有描述,见表7-8。铸球的金相组织直接影响铸球的力学性能和耐磨性,对于铬铁铸造磨球,常见的组织是基体+碳化物。不同的基体组织抵抗磨损的行为不同,同种基体组织,在不同工况条件和磨损类型下抗磨行为也不相同,如湿磨条件下对磨球的损耗更大,如采用相同的高铬铸铁球,分别在干磨、湿磨条件下研磨花岗岩(granite),干磨条件下球的损耗是(51±5) mg/cycle,湿磨损耗是(106~9) mg/cycle[24]。更有甚者,在腐蚀作用占主导地位的情况下,对于同样的矿物粉末,湿磨消耗的金属是干磨的10倍[25]。
磨球本身的硬度、韧性、尺寸、合金含量,球磨机内的酸碱状况、球磨机的直径、装载量、进料粒度等都会影响到磨球的损耗。表9为影响研磨介质磨损的因素[26]。因此,在磨球组织选择时,应考察和分析磨球的工况条件和磨损类型,并根据具体工况条件下的主要磨损机制和“使用性、经济性”原则,确定磨球的组织类型。
一般情况下,磨球主要有三种磨损失效机制:一种是磨粒切削磨损。对磨球表面施力,并有相对运动的磨粒,在法向力作用下嵌入表面,切向力则推动磨粒沿表面运动。在铬铁磨球中,碳化物是硬脆相,当其周围较软组织被磨掉而失去对它的围护作用时,孤立的碳化物被重复滑过的磨料切割和撞击脆断,致使硬脆相脱落。一种是冲击疲劳磨损。磨球受到反复撞击,相互之间滚动与滑动,在交变的压力和剪切力作用下引起交变的赫兹接触应力,在材料的亚表层产生最大交变切应力、接触区边缘产生峰值拉应力,导致在亚表层的脆性相、夹杂物或孑L洞处产生疲劳裂纹,裂纹扩展与交织,最终使磨球表皮剥落及磨损。若裂纹产生于较深部位,并沿脆性相和缺陷向内部扩展,形成较大的纵深裂纹。裂纹会合并延及表面,会使磨球表面成块脱落。另一种是冲击磨粒磨损,磨球在撞击磨粒时,受到冲击磨损。在冲击磨粒磨损中,铬铁磨球中碳化物可被冲击碎裂及脱落,同时基体组织也被凿削和短程切削而磨损,表10为磨损机制及在相应机制下抗磨的基体组织类型
[27]。目前国内比较缺乏对铸球显微结构与其耐磨性关系的更为深入、系统的研究。而只有对铸球的显微结构深入了解,才能对其耐磨性的高低有更深刻的认识。Webera K等人利用M·ssbauer谱研究了高铬铸铁的显微结构与其耐磨性的关系,其研究的三种高铬铸铁成分见表11,经1150℃退火4h,200℃回火2h后,合金B的晶相主要有:初生碳化物、二次碳化物、马氏体、残余奥氏体,见图4[9]。最后的研究表明,硬度不能精确反应高铬铸铁磨球的耐磨性(研磨水泥),更为重要的是磨球物相中马氏体的碳含量,马氏体中碳含量高,磨球耐磨性更好,同时,在残余奥氏体中低碳含量的残余奥氏体比例越多,则磨球的断裂韧性更好。1 000—1150℃等温退火4h,200℃回火2h,可以获得优化的铸球韧性及耐磨性[9]。
三、铸造磨球的生产
3.1 砂型铸造工艺
湿型手工造型生产铸球是最简单的砂型铸球生产方法,该方法生产效率低、劳动强度大,但工艺简单,投入少。我国20世纪80年代也曾经从原西德引入过水玻璃砂造型线,该生产线主要用于生产高铬铸球,是我国较早的铸球生产线。除此之外我国也曾引入过 DISA造型线,该线效率很高,100~200型/h,一型甚至可以铸出上百个球。但DISA线价格相对昂贵,投资规模很大,一般小型企业很难有这样的投资能力。
国内目前仍然有很多企业在利用砂型铸造工艺生产铸球,采用的主要是叠箱工艺,叠箱造型工艺的优点有:①补缩压头高,补缩效果好,易获得内部致密的磨球;②相对单层砂型工艺,可减少浇冒口体积,提高工艺出品率;③造型占地面积小,浇注速度快;④节约型砂。叠箱造型工艺除了具有普通砂型铸造的一些缺点外还有以下缺点:①对型砂的透气性要求较高;②由于浇注后液态金属的静压头较高,低层铸球易产生粘砂缺陷,表面粗糙[28]。
相关铸造企业的研究主要集中在如何提高叠铸生产效率,改善铸球质量的方面,冯日青等将叠铸工艺应用在高铬铸球的生产中,在φ60mm~φ100mm铸球生产中,铁液工艺成品率为71%-73.6%,且无缩孔或缩松铸造缺陷。工作的劳动强度降低,劳动生产率提高[29]。
对于生产应用中的大量的小直径磨球,除了采用普通单层砂箱和叠箱铸造两种形式外,研究人员研究出一种倾斜浇注串铸工艺,见图5。
磨球串铸工艺特性:①倾斜浇注,钢液由低向高逐层进入铸型,钢液流动路线短,每个铸件充型时间短;②位于铸型低处的铸件可由横浇道和直浇道补缩,位于高处铸件则由冒口补缩;③钢液形成顺序凝固,内侧磨球可得到浇道和冒口的补缩,避免了磨球出现缩孔、缩松等缺陷[30-32]。
3.2 金属型生产铸造磨球
金属型铸造与砂型铸造比较,在技术上与经济上有以下优点:①金属型生产的铸件,其力学性能比砂型铸件高,同样合金,其抗拉强度平均可提高约25%,屈服强度平均提高约20%,其抗蚀性能和硬度亦显著提高;②铸件的精度和表面光洁度比砂型铸件高,而且质量和尺寸稳定;③铸件的工艺收得率高,液体金属耗量减少,一般可节约15%-30%;④不用砂或者少用砂,一般可节约造型材料80~100%[33]。
金属型工艺非常适合于生产磨球,其最大优点是金属铸型冷却速度快,可细化磨球组织,显著提高磨球的耐磨性及抗破碎性能。美国早在1927年,IJ·Barton就申请了使用金属型生产制备钢、合金钢、白口铸铁、可锻铸铁材质的铸球专利,专利的金属型为一型4球[34]。金属型铸造也存在一些不足,如产品易出现冷隔、高温气孔、沟槽、皱皮等缺陷,且金属型笨重,工人劳动强度大,无法实行多组合铸造及机械化生产。
覆砂金属型是在型腔表面覆盖一定厚度砂层的金属型??杉趸褐淙此俣?,减少铸件因铸型引起的气孔等缺陷。覆砂金属型铸造工艺克服了金属型铸造和砂型铸造的缺点,保持了它们的优点,且实现了全自动化控制的流水线生产。
3.2.1 覆砂金属型用于高性能磨球生产
基于金属型的快速冷却的优点,在研制生产高性能的铸球时,往往采用覆砂金属型。如在生产研制马氏体球墨铸铁及贝氏体球墨铸铁磨球时,根据材料本身流动性好、收缩的特点,一般都选择覆砂金属型生产,这是利用了金属型的激冷作用,以增加石墨球数、降低偏析程度。生产出的马氏体球墨铸铁磨球的金相组织为:高碳隐针马氏体(70%-75%)+球状石墨+上贝氏体(25%-30%)+少量合金碳化物(<5%)+少量残余奥氏体。其表面硬度为HRC 55~57,表面与心部硬度差HRC2;通过工业性试验平均单耗为0.66k砂t原矿、破碎率<1%[35]。贝氏体球墨铸铁磨球的室温金相组织为:下贝氏体B+少量残留奥氏体Ar+少量的碳化物(≤5%)+石墨,HRC 50-58,表面与心部硬度差HRC2~4[36]。
少量合金碳化物(<5%)+少量残余奥氏体。其表面硬度为HRC 55~57,表面与心部硬度差HRC2;通过工业性试验平均单耗为0.66k砂t原矿、破碎率<1%[35]。贝氏体球墨铸铁磨球的室温金相组织为:下贝氏体B+少量残留奥氏体Ar+少量的碳化物(≤5%)+石墨,HRC 50-58,表面与心部硬度差HRC2~4[36]。
3.2.2 覆砂金属型磨球生产的工艺自动化
我国的一些科研单位和企业对金属型铸造磨球机械化、自动化生产线工艺进行了研究,相关的铸球金属型模具的专利不下百种。目前,不但成功实现了铸造磨球的机械化生产,而且有多家单位可以提供自动化铸球生产线。安徽宁国就有多家公司:安徽省宁国市南洋铁球有限公司、安徽省宁国新宁实业有限公司、宁国市志诚钢球模具有限公司、安徽省宁国市四方钢球模具有限公司等。国内还有其他一些企业,如郑州化方机械制造有限公司、浙江省机电设计研究院、河北省景县新华模具厂等。
覆砂金属型的工艺流程见图6[37],其工艺特点为:①有效控制冷却速度,改变覆砂厚度和金属型壁厚,可有效控制铸件的冷却速度;②能实现多组合铸造,覆砂金属型可利用覆膜砂流动性好的优点,用射砂机将型砂射人金属型腔内,一次性完成多组合模具的铸造,图7-8为两种常见的组合形式”;③覆砂金属型工艺的金属型寿命长,其使用寿命可达近万次而金属型铸造的金属型使用寿命仅千余次;金属型工作面有覆砂层,无须精加工,铸造面的铁质晶粒细化、组织精细、模具耐用;④覆砂金属型铸造工艺能实现铸球机械化,覆砂金属型的铸造工艺是一个循环的生产过程,是采用机械化来完成的,只要增加一些辅机配上自控系统就可以实现流水线生产[37]。
覆砂金属型工艺生产不同磨球产品需要不同的铸型和芯板,这样生产成本投入比较大。1t磨球生产成本比手工金属型生产成本要增加200~300元[37]。
3.3 消失模工艺生产铸造磨球
消失模铸造生产周期短、效率高,铸件精度高,适合铸造复杂结构铸件,工艺灵活,而且投资少、见效快,生产效率高;消失模的不足之处是铸件表面生皱皮、炭黑、夹杂及夹渣等缺陷,大平面易变形[39-40]。
图9是年产量为3 000~5 000t 或以上的奥贝球铁磨球,或低、中、高铬铸铁磨球,或其他抗磨合金磨球的消失模铸造磨球生产流程[14]。一般情况下,消失模铸造磨球尺寸在巾30mm~φ120mm。磨球直径<30mm,比较容易出现积碳、皱皮、夹渣(碳黑);磨球直径>120mm,磨球易出现中心缩松、缩孔、空心。不过也有研究人员做消失模工艺制备大尺寸磨球的研究,并取得了满意效果,如刘瑞丽等采用消失模铸造了外径为1 150mm、内径850mm,材质为ZG75CrMn NiMo大型铸钢球,消失模解决了用砂型铸造大型空心钢球壁厚不均的缺陷,而且能够铸造出磨球表面的小圆钉凸起[42]。
消失模铸造工艺生产磨球的优势有:落砂清理工作量减少了30%~40%,外观尺寸精确;干艺出品率高,达到68%~75%,生产效率是传统砂型工艺的1.5~2倍;应用消失模工艺生产磨球的综合成本低,具有明显的经济效益[43]。
四、结束语
在铸造磨球的生产、研发过程中,应充分利用计算机模拟技术的优势以优化铸球生产工艺,减少新产品试制成本和铸球的生产成本[5]。
铸造磨球相关的国家及行业标准中所列出的大多是铸铁磨球,而铸钢磨球作为铸造磨球中的一种,在某些领域还有一定的应用。其研究主要通过合金化及热处理来提高其性能,即通过合金化和热处理改变铸球组织,从而提高铸球耐磨性。高性能的铸钢铸球的金相组织基本都是贝氏体+马氏体+少量奥氏体,而最佳热处理丁艺就是为了获得这三种组织的最佳配比。
与铸钢磨球相比,铸铁磨球的实际应用领域更广,这点从相应的国家及行业标准中就能看出。国家标准GB/T 17455—2009《铸造磨球》中磨球被分为铬合金铸铁磨球及球墨铸铁磨球,与铸钢磨球不同,铸铁磨球的研究主要集中在不同铬含量磨球在不同领域应用情况及高性能CADI磨球的研发等方面。低铬多合金白口铸铁球的特点是铬含量低,价格较低廉。高铬与中铬多合金铸铁球由于含较高铬元素,其金相为马氏体基体亡分布着不连续的碳化物,而碳化物以(Cr,Fe)7C3为主,因而其宏观硬度很高(HRC 50以上),又有一定韧性,具有优良的耐磨性,大受电力、水泥行业欢迎:贝氏体或马、贝体球墨铸铁磨球的金相组织,是由马氏体、贝氏体和球状石墨良好配合而成,具有良好的淬透性和硬韧性,其耐磨度为普碳钢球的2.5~3倍,价格偏贵[23]。
铸球的金相组织直接影响铸球的力学性能和耐磨性,只有对铸球的显微结构深入了解,才能对其耐磨性的高低有更深刻的认识。国内目前比较缺乏对铸球显微结构与其耐磨性关系的更为深入、系统的研究。
国内对于铸造磨球的研发应在以下方面加以重视。
(1)根据不同—L:况条件和磨损类型,以最优化的成本研制适合的铸造磨球;
(2)高校、科研机构应加强对铸造磨球耐磨性及力学性能与其显微组织的相关性的研究;
(3)进一步研发以更低的成本生产高性能的CADI磨球;
(4)对铸造磨球在不同丁况下的磨损机理进行更为深入、系统的研究,为相关的应用企业提供最佳的铸造磨球选择,以达到最大限度地减少磨球消耗、降低水泥、矿山、电力等部门生产成本的目的。
目前国内生产铸造磨球的下:工艺方法有砂型铸造厂艺、覆砂金属刮铸造工艺、消失模铸造工艺等。每种工艺都有各自的特点,如湿型手工造型生产铸球工艺简单,投入少;覆砂金属型工艺能实现铸球机械化生产;消失模铸造工艺生产磨球的优势是落砂清理工作量减少厂30%~40%,外观尺寸精确;工艺出品率高,达到68%~75%:铸造磨球生产厂家应结合本地情况,选择合适的铸球生产工艺。
?。ㄕ浴吨臁罚?/p>
附件下载:

-
地址:济南市解放路134号 电话:0531-86401781 / 86952422 传真:0531-86465075
邮箱:foundry-shandong@163.com 邮编:250013
版权所有 © 山东省铸造协会 鲁ICP备2021002429号
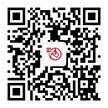
官方公众号